The principle research and production of clamp type vortex flowmeter is a volumetric flowmeter for measuring the volume flow rate, standard condition volume flow rate, or mass flow rate of gases, vapors, or liquids. Mainly used for flow measurement of industrial pipeline media fluids, such as gases, liquids, steam, and other media.
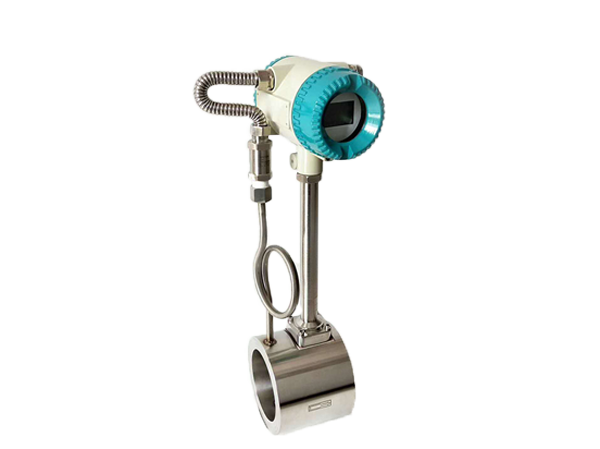
Manufacturer of clamp type vortex flowmeter
Nominal diameter: DN15~DN300mm
Accuracy level: ± 1.0% for liquids, ± 1.5% for gases (vapors), ± 2.5% for insertions
Structural form: integrated, split, temperature and pressure compensation
Applicable media: liquid, gas, saturated steam, superheated steam
The flange clamped vortex flowmeter is applied in the process measurement and energy-saving management of various low viscosity single-phase fluids such as liquids, gases, steam, etc. in industries such as petroleum, chemical, metallurgical, mechanical, food, papermaking, as well as urban pipeline heating, water supply, gas, etc.
There is a big difference between flange clamping and flange connection. Flange connection is a type where the flange is welded and integrated with the body as a whole. During installation, the flanges at both ends of the flowmeter and the flange on the pipeline can be directly fixed with bolts to achieve use. Flange connection is also very common. The body of the flange clamped vortex flowmeter does not include a flange, and the entire set includes flange plates, bolts, nuts, and gaskets. During installation, the flange gaskets are connected and fixed to the flange welded to the pipeline through bolts and nuts before being put into use.
The clamp type vortex flowmeter is designed based on the Karman vortex theory. When the fluid flows through a non streamlined baffle, vortices are alternately generated on both sides of the baffle. The frequency of these vortices is proportional to the average flow velocity of the fluid in the pipeline, and therefore proportional to the flow rate. That is, in the formula Q=f/k, Q is the instantaneous flow rate f is the vortex street frequency k is the instrument coefficient. The frequency of the vortex generator is only related to the flow velocity of the measured medium and is independent of the density/viscosity of the measured medium.
The instrument coefficient is determined by the geometric dimensions of the measuring tube of the instrument and is independent of the sensor and converter. The pressure changes caused by the alternately generated vortices are sensed by sensors, and the frequency signal is detected by electronic circuits and sent to a microprocessor for calculation and processing, achieving on-site digital display and 4-20mA current output.
The flange clamped vortex flowmeter is a commonly used structural form, and its body does not have a connecting flange. When connected to the pipeline, the flowmeter is clamped between two dedicated flanges and then fastened with bolts. Its characteristics are small size, simple and compact structure. We also provide dedicated flanges and fastening bolts, so the installation cost is low and the installation is very convenient.
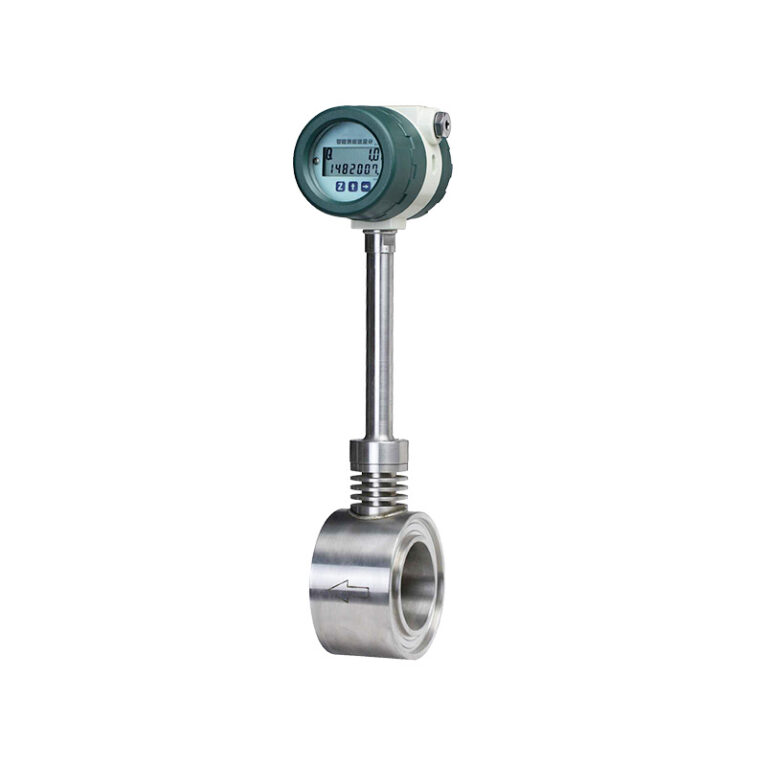
Advantages and characteristics of clamp type vortex flowmeter:
- Easy to install and maintain; The structure is simple and sturdy, with no movable parts, making it highly reliable for long-term operation;
- Wide range, with a range ratio of up to 1:15; Low pressure loss, low operating costs, and greater energy-saving significance;
- Wide application range, capable of measuring liquids, gases, and vapors; The verification cycle is long, usually two years;
- Within a certain Reynolds number range, the output signal is not affected by the physical properties and composition changes of the measured medium, and the instrument coefficient is only related to the shape and size of the vortex generator. After replacing the accessories, there is generally no need to recalibrate the instrument coefficient;
- It can be displayed on-site, transmitted over long distances, and connected to computer control systems; The detection probe does not directly contact the measured medium, resulting in more stable performance.
Technical parameters of clamp type vortex flowmeter
property | Technical parameter |
Nominal diameter | DN15~DN300 |
Nominal pressure | 1.6Mpa、2.5Mpa、4.0Mpa。Higher pressure can be customized |
Medium temperature | -4℃~+250℃ -40℃~+350℃(High temperature type) |
Body material | 304SS Stainless steel |
accuracy level | Tube type: ±1.0%, ±1.5%/ Insert type: ±2.5% |
Range ratio | 1:10、1:15、1:20 |
Working power supply | External power supply: +24VDC±15%, suitable for 4 ~ 20mA, pulse, RS485 internal power supply: 1 set of 3.6v lithium battery, can work for more than two years |
Signal output | Simulate 4 ~ 20mA signal and pulse signal |
Communication output | RS485 communication, HART protocol |
Ambient temperature | -20℃~+60℃ |
Relative humidity | 5%~90% |
Atmospheric pressure | 103kpa±10 |
Several key factors for selecting vortex flowmeter:
- Medium temperature. A temperature of around 300 ° C is considered a critical value, and even higher temperatures may require high-temperature resistant vortex streets and piezoelectric vortex streets.
- Medium pressure, which mainly applies to gases and vapors.
- Medium flow range, commonly used flow rates.
- The degree of corrosiveness of the medium.
- Continuity or intermittency of pipeline operation.
- Instrument installation environment temperature.
- Are there any high-power devices around the instrument.
- There is a problem with the direction of the instrument power cord.
We also need to confirm the following parameters:
- Selection of instrument power supply mode (battery power supply, 24V, 220V).
- Instrument signal output: 4-20mA, pulse output.
- Instrument display mode (with or without display),
- Instrument accuracy level (1.5, 1).
- When designing a steam flowmeter, it is necessary to consider whether the flow range is within the instrument range, and pay attention to the measurement impact of small flow on the meter to determine the appropriate diameter of the flowmeter.
- Do you need to equip with integrated temperature and pressure compensation, etc.
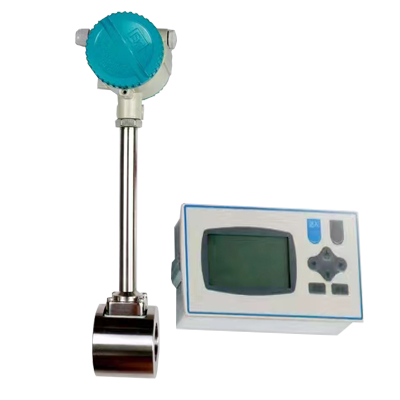
Installation environment requirements for flange clamped vortex flowmeter:
- Try to avoid strong electrical equipment, high-frequency equipment, and strong switching power supply equipment as much as possible. The power supply of the instrument should be separated from these devices as much as possible.
- Avoid direct effects from high-temperature heat sources and radiation sources. If installation is necessary, insulation and ventilation measures must be taken.
- Avoid high humidity and strong corrosive gas environments. If installation is necessary, ventilation measures must be taken.
- Vortex flow meters should be avoided from being installed on pipelines with strong vibration as much as possible. If installation is necessary, pipeline fastening devices must be installed at 2D upstream and downstream locations, and anti vibration pads must be added to enhance the anti vibration effect.
- It is better to install the instrument indoors. When installing outdoors, attention should be paid to waterproofing. Special attention should be paid to bending the cable into a U-shape at the electrical interface to prevent water from entering the amplifier housing along the cable.
- There should be ample space around the instrument installation point for wiring installation and regular maintenance.