The flange connected vortex flowmeter is a volumetric flowmeter developed and produced based on the Karman vortex principle to measure the volumetric flow rate, standard condition volumetric flow rate, or mass flow rate of gases, vapors, or liquids. Mainly used for flow measurement of industrial pipeline media fluids, such as gases, liquids, steam, and other media.

Manufacturer of flange type vortex flowmeter
Nominal diameter: DN15~DN300mm
Accuracy level: ± 1.0% for liquids, ± 1.5% for gases (vapors), ± 2.5% for insertions
Structural form: integrated, split, temperature and pressure compensation
Applicable media: liquid, gas, saturated steam, superheated steam
The flange connected vortex flowmeter can be widely used for measuring gas, liquid, and steam flow in small and medium-sized pipelines in various industries. Its body comes with a connecting flange. When connecting to the pipeline, the flowmeter flange can be connected to the pipeline flange and then tightened with bolts. Its characteristics are simple structure and easy installation.
The flange connected vortex flowmeter is based on the theories of Karman and Strouhal regarding the generation of vortices and the relationship between vortices and flow rates to measure the flow rates of steam, gas, and low viscosity liquids. A triangular column is inserted vertically into the table body, which is the generator of vortices. When a medium flows through the table body, regular Karman vortices with opposite directions are alternately generated behind the triangular column. The separation frequency F of the vortices is proportional to the flow velocity V of the medium. By detecting the number of vortices through the sensing head, the fluid velocity can be calculated, and then the volumetric flow rate of the measured medium can be calculated based on the diameter of the body.
Configuration of flange connected vortex flowmeter:
- Temperature and pressure compensation:
When measuring the mass flow rate of steam, due to its density changing with temperature and pressure, it is necessary to compensate for the steam at any time. A mass flow measurement system is composed of a platinum thermistor, pressure transmitter, and vortex sensor. Other media can be combined into a mass flow measurement system according to actual conditions.
- Selection of intelligent flow integrator:
When measuring saturated steam, a flow integrator with temperature automatic compensation density or pressure automatic compensation density should be selected; When measuring superheated steam, a flow integrator with temperature and pressure compensation for density should be selected; Adopting remote communication, the intelligent flow integrator should consider having RS485 or RS232 communication interfaces; When required to form a flow measurement system with the control system, the intelligent flow integrator should be equipped with a 4-20mA standard current signal output interface;
When necessary, a backup power supply should be configured so that the instrument can measure normally in the event of a sudden power outage. When needed, an instrument box should be configured to place the intelligent flow integrator inside. The instrument box should be equipped with a lock to prevent the setting parameters of the intelligent flow integrator from being adjusted arbitrarily, and it should have anti-theft function. At the same time, a protective circuit should be installed inside the instrument box to protect the intelligent flow integrator.
- Remote monitoring: When multiple measurement points are required, with a large distribution area, and real-time monitoring is needed, GSM/GPRS communication network or wireless private network remote flow monitoring system can be used to achieve real-time monitoring and management of the flow of each pipeline.
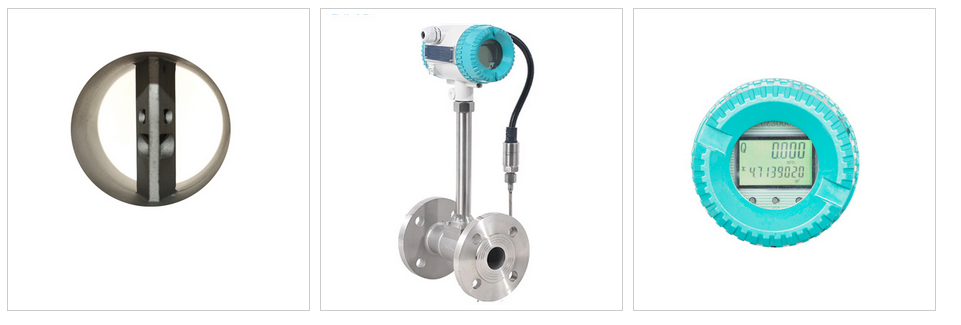
Advantages of flange connected vortex flowmeter
- The structure is simple and sturdy, with no movable parts, high reliability, and very reliable for long-term operation;
- Easy installation and convenient maintenance;
- The detection sensor does not directly contact the measured medium, with stable performance and long service life;
- The output is a pulse signal proportional to the flow rate, with no zero drift and high accuracy;
- Wide measurement range, with a range ratio of up to 1:10;
- Less pressure loss, lower operating costs, and more energy-saving significance;
- Within a certain Reynolds number range, the output signal frequency is not affected by the physical properties and composition changes of the fluid, and the instrument coefficient is only related to the shape and size of the vortex generator. When measuring the fluid volume flow rate, there is no need to compensate, and after replacing accessories, there is generally no need to recalibrate the instrument coefficient;
- Widely applicable, the flow rates of steam (saturated steam), gases (air, oxygen, nitrogen, coal gas, natural gas, gas, hydrogen, liquefied petroleum gas, hydrogen peroxide, flue gas, methane, butane, chlorine, gas, biogas, carbon dioxide, nitrogen, acetylene, phosgene, oxygen, compressed air, argon, toluene, benzene, xylene, hydrogen sulfide, sulfur dioxide, ammonia), steam, liquids, and water, liquids (water, high-temperature water, oil, food liquids, chemical liquids, etc.), liquids, and gases can be measured.
Technical Parameter
Nominal diameter | DN15~DN300mm |
Measuring medium | Liquid, gas, saturated steam, superheated steam |
accuracy level | Liquid ±1.0%, gas (steam) ±1.5%, plug-in ±2.5% |
Working pressure | 1.6MPa,2.5MPa,4.0MPa,6.4MPa |
Medium temperature | Ordinary type -40 ~ 150℃ Medium temperature type -40 ~ 250℃ High temperature type -40 ~ 350℃ |
Output signal | Three-wire voltage pulse, low level 0 ~ 1V, high level > 4V, duty cycle 50%; Two-wire system standard current 4 ~ 20mA; Three-wire system standard current 0 ~ 10mA |
Working environment | -35℃ ~ +60℃, humidity ≤95%RH |
Working power supply | DC12V;DC24V |
Shell material | Carbon steel, stainless steel |
Precautions for selecting vortex flowmeter:
The selection of vortex flowmeter should be based on the physical and chemical properties of the measured fluid medium. By considering the characteristics of the medium, the diameter, flow range, lining material, electrode material, and output current of the vortex flowmeter should be selected to adapt to the properties of the measured fluid and the requirements of flow measurement.
- Accuracy issue selection
In terms of precision level, for instruments, the higher the precision level, the higher the price, and the correct choice is necessary to achieve cost-effectiveness. For example, in situations such as trade settlement, product handover, and energy measurement, higher accuracy levels such as 1.0, 0.5, or higher should be selected; For process control applications, choose different accuracy levels according to control requirements; In some cases where only the process flow rate needs to be detected without precise control and measurement, a slightly lower accuracy level, such as 1.5, 2.5, or even 4.0, can be selected. In this case, a low-cost plug-in vortex flowmeter can be used.
- Measurable medium
Each type of vortex flowmeter has a flow range limit, and the diameter of the instrument should be as consistent as possible with the pipeline. The selection of instrument specifications (caliber) may not necessarily be the same as the process pipeline, and should be determined based on whether the measured flow range is within the flow rate range. That is, when the pipeline flow rate is too low to meet the requirements of the flow instrument or the measurement accuracy cannot be guaranteed at this flow rate, the instrument port diameter needs to be reduced to increase the flow rate inside the pipeline and obtain satisfactory measurement results.
- Selection of Vortex Flow Transmitter
In practical applications, it is generally considered that the flow rate of saturated steam measured must not be lower than the lower limit of the vortex flowmeter, which means that the fluid velocity must not be lower than 5m/s. Choose vortex flow transmitters with different diameters based on the amount of steam used, rather than selecting the transmitter diameter based on the existing process pipeline diameter.
- Selection of pressure compensation pressure transmitter
Due to the long saturated steam pipeline and significant pressure fluctuations, pressure compensation must be used. Considering the correspondence between pressure, temperature, and density, only pressure compensation is required for measurement. As the saturated steam pressure in the pipeline is in the range of 0.3-0.7MPa, the range of the pressure transmitter can be selected as 1MPa.
- Display instrument selection
Intelligent flow display instrument with voltage stabilization compensation, instantaneous flow display, and cumulative flow calculation functions. This item and the fourth item above are actually many of them combined. It is more convenient to directly purchase the integrated temperature and pressure compensation.