Metal float flowmeter (also known as metal rotor flowmeter) has the characteristics of simple structure, reliable operation, wide applicability, high accuracy, and easy installation. Compared with glass rotor flow meters, this series of flow meters has the characteristics of high pressure resistance, high temperature resistance, strong sense of safety, and concise readings. And it can be applied to flow measurement of opaque and corrosive media.
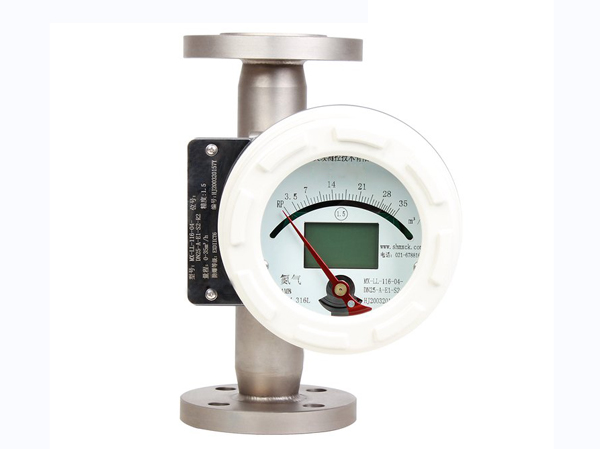
Manufacturer of intelligent metal float flowmeter
- Sturdy, concise, compact, and reliable design
- Imported intelligent transmitters ensure stable and accurate data transmission signals
- New magnetic steel coupling structure and eddy current braking design ensure more stable data transmission signals
- Gas damping device, ensuring stable measurement of low-pressure or fluctuating media, insulation or heat tracing jacket, low pressure loss design
- Multiple functions: on-site indication, accumulation, alarm, remote transmission, etc
- Suitable for various explosion-proof applications (intrinsic safety Ex ia Ⅱ CT1~T6 Ga, explosion-proof Ex d IIC T1~T6 Gb)
- Multiple signal outputs: 4-20mA electrical signal; Switch signal
- HART communication, PROFIBUS PA communication
- Suitable for various installation forms of pipelines
Structural principle of metal float flowmeter
The flow detection element of a metal float flowmeter consists of a vertically expanding conical tube and a float group that moves up and down along the axis of the conical tube. When the fluid being tested passes through the annular gap 3 formed by the cone tube 1 and the float 2 from bottom to top, a differential pressure is generated at the upper and lower ends of the float, forming a force for the float to rise. When the upward force on the float is greater than the weight of the float immersed in the fluid, the float rises, and the annular gap area increases accordingly. The fluid flow velocity at the annular gap immediately decreases, and the differential pressure between the upper and lower ends of the float decreases. The upward force acting on the float also decreases until the upward force is equal to the weight of the float immersed in the fluid, and the float stabilizes at a certain height. The height of the float in the cone tube corresponds to the flow rate it passes through.
Advantages and disadvantages of metal float flowmeter
Metal float flowmeter is used for small diameters and low flow rates. Commonly used instrument diameters are below 40-50mm, with a minimum diameter of 1.5-4mm. Suitable for measuring low flow rates and small flow rates, taking liquids as an example, the nominal diameter of a glass tube float flowmeter with a diameter of less than 10mm for full flow rate is only between 0.2-0.6m/s, and even less than 0.1m/s; Metal tube float flow meters and glass tube float flow meters with a diameter greater than 15mm are slightly higher, with flow rates between 0.5-1.5m/s.
Float flow meters can be used for lower Reynolds numbers, using floats with viscosity insensitive shapes. As long as the Reynolds number at the flow annulus is greater than 40 or 500, the flow coefficient remains constant when the Reynolds number changes, meaning that changes in fluid viscosity do not affect the flow coefficient. This value is far below the minimum Reynolds number requirement of 104-105 for standard orifice plate and other throttling differential pressure instruments.
Most float flowmeters do not require an upstream straight pipe section, or in other words, do not have high requirements for the upstream straight pipe section.
Float flow meters have a wide flow range, generally 10:1, with a minimum of 5:1 and a maximum of 25:1. The output of the flow detection component is close to linear. Low pressure loss.
The glass tube float flowmeter has a simple structure and is inexpensive. As long as the flow indicator is convenient to use on site, the disadvantage is the risk of glass tubes being fragile, especially for unguided floats used for gas.
The metal tube float flowmeter has no risk of cone tube rupture. Compared with glass tube float flow meters, it has a wide range of temperature and pressure usage.
Most structural float flow meters can only be used for pipeline installation with vertical flow from bottom to top.
The application of float flow meters is limited to small and medium-sized pipe diameters. Ordinary full flow float flow meters cannot be used for large pipe diameters. The maximum diameter of glass tube float flow meters is 100mm, while metal tube float flow meters are 150mm. For larger pipe diameters, only shunt type instruments can be used.
When the fluid used is different from the factory calibrated fluid, flow indication correction should be performed. Float flow meters for liquids are usually calibrated with water, while those for gases are calibrated with air. If the actual fluid density and viscosity are different, the flow rate may deviate from the original division value and require conversion correction.