Thermal mass flowmeter is a flow meter that measures fluid mass flow by utilizing the temperature field changes generated when the fluid flows through a pipeline heated by an external heat source, or by measuring the energy required for the fluid temperature to rise by a certain value when heating the fluid and the relationship between the fluid mass and the fluid mass.
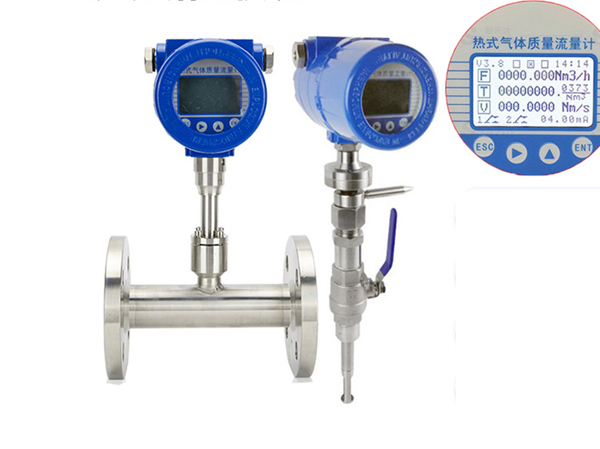
Manufacturer of intelligent thermal gas mass flowmeter
● Range accuracy: ± 1% reading ± 0.5% full range ● Pipe diameter range: 10mm~6000mm
● Range ratio: 1000:1 (depending on the calibrated flow range) ● Sensor material: 316 stainless steel, Hastelloy, titanium
Flow range: 0-120Nm/s (20 ℃, 101.33KPa)
● Environmental temperature:- 40 ℃~+85 ℃ ● Voltage resistance: 16MPA
Applicable medium: Suitable for various types of single or mixed gases. Containing dust, sand, moisture, and various corrosive gases
Application scenarios: Widely applicable to the measurement and control of superheated steam, saturated steam, compressed air and general gases (oxygen, nitrogen, hydrogen, natural gas, coal gas, etc.), water and liquids (such as water, gasoline, alcohol, benzene, etc.) in industries such as petroleum, chemical, metallurgical, thermal, textile, paper, etc
Principle of Thermal Mass Flow Meter
Thermal Mass Flowmeters (TMF), commonly known as thermal mass flow meters, are flow meters that measure fluid mass flow by utilizing the temperature field changes generated when fluid flows through a pipeline heated by an external heat source, or by using the relationship between the energy required for the fluid temperature to rise by a certain value during fluid heating and the fluid mass. It is generally used to measure the mass flow rate of gases. Has low pressure loss; Large flow range; High precision, high repeatability, and high reliability; No movable parts and can be used for extremely low gas flow monitoring and control The use of heat (or temperature) changes from heated fluids to measure the mass flow rate of fluids has a long history. Early TMF directly placed heating coils and temperature measuring elements in contact with the fluid, making it a contact flowmeter. However, due to its inability to solve problems such as nozzle corrosion, wear, and explosion prevention, its industrial application was greatly limited. Thomas flowmeter is a representative of this type of flowmeter, mainly used to measure the mass flow rate of gases with large flow rates; In the 1950s, a boundary layer flowmeter that did not come into contact with fluids was proposed, overcoming the shortcomings of contact flowmeters. However, the measurement results were easily affected by medium parameters such as thermal conductivity, specific heat capacity, viscosity, etc., and could be used to measure larger liquid flow rates; In the 1970s, the thermal distribution type TMF based on measuring fluid temperature distribution developed rapidly both domestically and internationally due to its unique advantages. It was used to measure small gas flow rates. With the development of technology, after redesigning the flowmeter structure, an immersion type TMF was proposed based on the contact flowmeter, which also developed rapidly and can be used to measure gas flow rates with larger diameters. In summary, TMF is a direct mass flowmeter mainly used to measure gas mass flow rate.
Thermal mass flowmeter: an instrument that uses the principle of heat transfer to detect flow, that is, an instrument that measures flow by utilizing the heat exchange relationship between the fluid in the flow and the heat source (the object heated in the fluid or the heating element outside the measuring tube). I used to practice weighing thermal flow meters.
Basic principle: Measuring gas flow by measuring the cooling effect when gas flows through the heating element inside the flowmeter. There are two thermal resistance elements in the measuring section through which gas passes, one of which serves as a temperature sensor and the other as a heater. The temperature sensing element is used to detect gas temperature, while the heater maintains a constant temperature difference between its temperature and the temperature of the measured gas by changing the current. As the gas flow rate increases, the cooling effect becomes greater, and the current required to maintain a constant temperature between the thermal resistors also increases. This heat transfer is proportional to the gas mass flow rate, that is, there is a corresponding functional relationship between the supply current and the gas mass flow rate to reflect the gas flow rate.
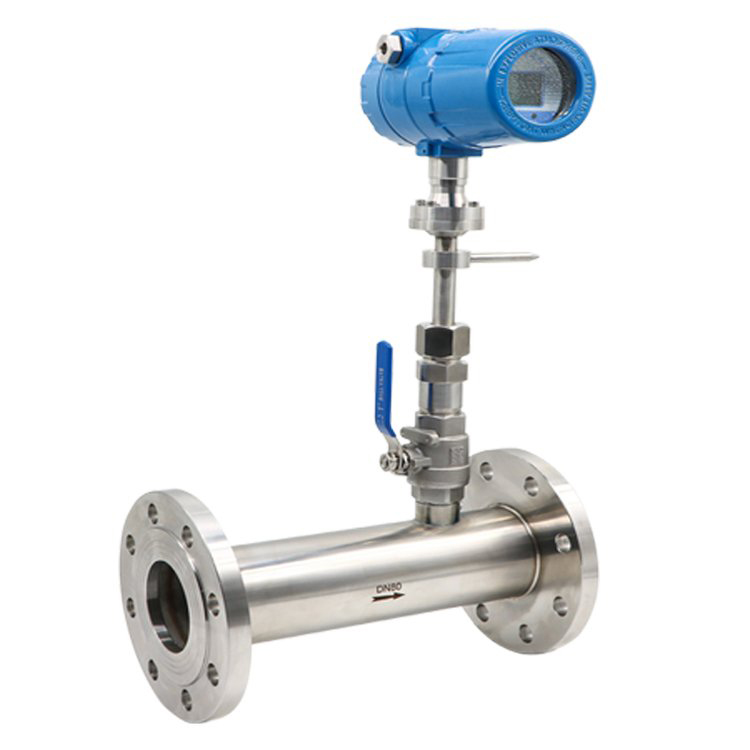
Classification of thermal mass flow meters
Thermal mass flow meters can be divided into two types based on the different heat sources and temperature measurement methods: contact type and non-contact type.
- Contact type thermal mass flowmeter
The heating element and temperature measuring element of this mass flowmeter are placed inside the pipeline of the measured fluid, in direct contact with the fluid, and are often referred to as Thomas flowmeters, suitable for measuring large mass flow rates of gases Due to the direct contact between the heating and measuring elements and the measured fluid, the elements are susceptible to fluid corrosion and wear, which affects the measurement sensitivity and service life of the instrument. It is not suitable to use contact type when measuring high flow velocity and corrosive fluids. - Non contact thermal mass flowmeter
The heating and temperature measuring elements of this flowmeter are placed outside the fluid pipeline, without direct contact with the measured fluid, overcoming the disadvantages of contact type.
Application of Thermal Mass Flow Meter
- Measurement of gas flow in steel plants and coking plants;
- Boiler air flow rate, measure secondary air volume;
- Measurement of smoke flow rate emitted from chimneys;
- Waterfall gas flow measurement in water treatment;
- Gas flow measurement during the production process of cement, cigarettes, and glass factories;
- Compressed air flow measurement;
- Measurement of gas flow rates for natural gas, coal gas, liquefied gas, torch gas, hydrogen, and other gases.
Advantages of Thermal Mass Flow Meter
Thermal mass flowmeter can measure small flow rates at low flow rates (gas 0.02~2m/s); Immersion thermal mass flow meters can measure low to medium to high flow rates (gas 2-60m/s), while plug-in thermal mass flow meters are more suitable for large pipe diameters.
Thermal mass flow meters have no moving parts, and thermal distributed instruments without diversion pipes have no flow blocking components, resulting in minimal pressure loss; Thermal distributed instruments and immersion instruments with diversion pipes, although equipped with flow blocking components in the measuring pipeline, have minimal pressure loss.
The performance of thermal mass flow meters is relatively reliable. Compared with deductive mass flow meters, it does not require temperature sensors, pressure sensors, and computing units, only flow sensors, simple composition, and low probability of failure.
Thermal distributed instruments are used for diatomic gases such as H2, N2, O2, CO, NO, which are close to ideal gases. They do not need to be specifically calibrated with these gases, but can be calibrated directly with air. Experimental results have shown that the difference is only about 2%; For single atom gases such as Ar and He, multiply by a coefficient of 1.4; It can be converted to specific heat capacity for other gases, but the deviation may be slightly larger.
The specific heat capacity of a gas varies with pressure and temperature, but small changes around the temperature and pressure used can be considered constant.